Методы формирования резьбы
Как правило, резьбу нарезают (накатывают) на завершающих этапах изготовления детали. Это говорит о важности процесса, потому что в изготавливаемую деталь уже вложены определённые финансовые средства и разного рода ошибки могут обойтись довольно дорого.
То есть, говоря о формировании резьбы, такие вопросы как производительность и цена не всегда в приоритете. Как правило, основное внимание сосредоточено на ее качестве. По обыкновению, для формирования резьбы используют три метода.
Нарезание
Это наиболее используемая операция, и в 90% случаев используют именно его. В ходе выполнения этой операции используют режущий инструмент (метчики, плашки) врезающиеся в материал заготовки. Конструкция этого инструмента спроектирована для конкретного диаметра и формы резьбы, а скорость подачи инструмента должна отвечать шагу резьбы.
Инструмент подают по оси Z, это обеспечивает простое программирование операции. Используемые инструменты отличаются друг от друга – геометрией, протяжённостью заборной части, допусками и углами режущей части.
Накатывание
Накатывание – формирование внутренней резьбы, путем выдавливания материала заготовки для получения требуемой формы. Для этой операции применяют инструмент, внешне схожий с метчиком, но обладающий другой конструкцией. Резьба после накатывания обретает более высокие прочностные характеристики, это обусловлено тем, что изменяется структура материала заготовки, а это приводит к наращиванию твердости заготовки. Но выбирая накатку, технолог должен помнить, ее можно использовать на ковких материалах и нельзя использовать при работе с чугуном.
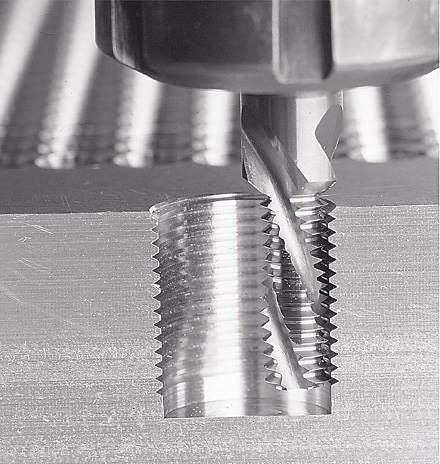
Фрезерование
Фреза повтояет форму резьбы, но размер нарезаемой резьбы контролирует станок.
Фрезерование – это резание заготовки материала с вращающимся инструментом (фрезой). Режущая часть которой повторяет профиль резьбы. Размер фрезы несколько меньше диаметра отверстия. То есть для получения резьбы оператор станка вводит фрезу в отверстие, синхронно подавая ее по оси Z и формируя при этом резьбу.
Применение фрезы влечет за собой сложности в написании управляющей программы, так как система управления станком держит под контролем размер резьбы, и настройку размера выполняют внесением корректив в программу. При использовании нарезки и накатывания вместо этого просто необходим инструмент требуемого размера.
Сопоставление надежности процессов
Нарезание – надежный и простой способ создания резьбы. Однако для достижения стабильного результата необходимо выбрать правильный метчик, подходящий для конкретной задачи.
Удаление стружки – это серьезная проблема, особенно в отношении обработки глухих отверстий. Для удаления стружки требуется подобрать метчик соответствующей конструкции, поэтому многие изготовители предлагают большой выбор метчиков с разной геометрией.
Другой не менее серьезный вопрос – поломка и застревание инструмента в отверстии. Так как головка метчика буквально вворачивается в заготовку, вытащить сломанную часть довольно сложно. Для этого может потребоваться дополнительная операция на другом станке, например на электроэрозионном.
Номенклатура инструмента для накатывания значительно меньше, чем номенклатура метчиков, это сопряжено с тем, что нет необходимости в удалении стружки. В сравнении с метчиками, накатники обладают стержнем большего размера, что увеличивает их прочность. Сломанный инструмент для накатывания также сложно вытащить из отверстия, но дело в том, что они ломаются реже, из-за большего размера стержня.
В сравнении с нарезанием, накатывание имеет некоторые ограничения, например связанные с маркой материала и диаметром резьбы. В технической документация некоторых компаний и даже целых отраслей можно найти указания, налагающие запрет на накатывание резьбы на некоторых деталях.
Это сопряжено с тем, что после накатывания на дне отверстия формируется углубление, его называют за свой внешний вид «рыбий рот». Хотя это углубление не влияет на качество резьбы, накатывание не применяют для продукци медицинского и пищевого назначения, т. к. в этом углублении могут размножаться микроорганизмы, а простерилизовать ее довольно сложно.
Можно смело утверждать, что фрезерование самый гибкий из рассматриваемых операций. Инструмент формирует профиль и наклон резьбы, что позволяет получать резьбу любого диаметра – главное, чтобы ее профиль и наклон не изменялись. Например, при помощи одной фрезы можно получить резьбу диаметром 1′′-8 и 11⁄2′′ -8 по стандарту UN. При этом в диаметр резьбы можно вносить коррективы, чтобы она отвечала нормам допусков, или возмещать износ фрезы, таким образом продляя время эксплуатации.
Диаметр стержня фрезы меньше, чем диаметр метчика или накатника, но фрезерование и не нуждается в использовании инструмента с большой прочностью. Диаметр инструмента лежит в пределах 70-80% размера резьбы, и даже если инструмент сломался, малый размер позволяет вытащить его из отверстия и после установки нового инструмента продолжить процесс обработки.
Сопоставляя между собой нарезание и накатывание можно сделать вывод, что накатывание более надежно, т. к. в ходе его выполнения не формируется стружка. Ко всему прочему вероятность поломки метчика выше, вследствие меньшего размера стержня. Однако опыт показывает, что максимальную надежность обеспечивает фрезерование.
Компания Сварог осуществляет формирование резьбы изготавливаемых деталей с использованием высокопроизводительного оборудования с полным соблюдением технологического процесса и гарантией качества готовых изделий.